Core Bit Trouble Shooting
The majority of issues with diamond tools arise due to one of the following reasons:
The tool wasn’t matched to the job, the tool wasn’t used correctly or the machine is faulty.
For urgent assistance please contact our head office.
E: sales@syntecsolution.com
T: (866) 360-3607 or (760) 737-7407
F: (760) 737-6718
Warning:
Never use a bent barrel.
Straight segments are vital for precision cutting. Deformation may occur due to excessive pressure when drilling through rebar, insufficient coolant, or tough materials.
– Replace core bit and decrease pressure when cutting rebar.
– Increase water supply.
– Select a suitable core bit.
The core bit may become lodged in the drill hole when the material or patches within it are excessively hard, filling the hole with rubble from broken-off segments. This issue is compounded by inadequate side clearance on the core bit, preventing the segments from operating effectively.
– Immediately stop the drill to prevent any further damage or complications.
– Reverse the drill by spinning the core bit counter-clockwise. Note that this option is only applicable if the drill has a reverse feature.
– Remove the drill and attempt to dislodge the core bit by creating wedges around the circumference of the core barrel. Add lubricant, rock it side to side, or use a core bit extractor.
– Flush out the drill hole thoroughly before proceeding with further drilling, and ensure a sufficient coolant supply. Check the side clearance and replace the core bit if necessary.
Over time, the bond of a core bit wears away, enabling the diamonds to continue cutting. However, if the bond doesn’t wear away as intended, the diamonds remain concealed, causing the core bit to slow down until it eventually stops cutting gradually. This smoothing of the core bit’s cutting edge is known as glazing or polishing. Various factors can contribute to a core bit not cutting efficiently. Identifying the problem and its root cause is essential to applying the correct solution.
– Reduce RPM speed.
– Increase drilling pressure and decrease speed of rotation.
– Rectify or sharpen the core bit using a soft concrete block or abrasive stone to expose diamonds by drilling 3-5 holes with ample water to uncover new diamonds.
– Alternatively, adding a small amount of builder’s sand down the hole can achieve the same effect. Run the drill slower with reduced downward pressure, allowing an abrasive paste to form and sharpen the segments. If the issue persists, consider selecting a core bit with a softer bond.
– Decrease the water flow and ensure even distribution. The water should appear milky or cloudy.
– Tighten anchor and ensure stability.
– Ensure that the machine’s horsepower is sufficient and matches the drilling diameter.
– Adjust the carriage on the side to reduce play.
– Check inside of core bit.
The core may become stuck in the core barrel due to insufficient water to remove the slurry or if the core barrel is dented from previous attempts to remove stuck pieces by hammering on it.
– Increase water flow after removing bit and driving core out with a spike through the hub. Remove debris.
– Replace the core bit.
Warning:
Never use a cracked barrel
When the core bit is subjected to extreme pressure and metal fatigue, the barrel can eventually crack.
– Reduce pressure.
– Use a core bit with a softer bond.
When utilised incorrectly, the core bit’s segments may crack, indicating that the bond is too hard and the drill is moving while drilling.
Decrease the RPM or use a core bit with a softer bond.
Hold the drill firmly or mount it on a stand.
With the correct application, core bits provide a clean cut. If the material is chipping, possible causes include the core bit’s bond not being suitable for the material, insufficient coolant reaching the drilling area, incorrect RPM or the material or drill is moving.
– Select a bond that suits the material.
– Ensure the water supply is adequate.
– Alter speed in line with recommendations.
– Ensure the material is held in place using clamps or apply a drill stand.
Incorrect specifications can result in over-exposure of diamonds in a segment, leading to excessive wear and impacting the bit’s lifespan. This may occur due to insufficient coolant, low RPM, excessive motor power, a vibrating drill.
– Check and Increase water supply.
– Increase speed within recommended RPM.
– Adjust machine power to match core bit diameter.
– Ensure drill rig/stand is secured firmly and stable. Check bearings, rollers, spindle and drill, etc. Tighten carriage guides.
– Choose core bit with the right specifications.
Excessive wear can cause the tube to thin, diminishing the lifespan of the bit. This wear may be exacerbated by factors such as a vibrating drill, a warped or misaligned barrel, or a cluttered hole with debris.
– Replace barrel.
– Ensure the drill rig is secured firmly. Check bearings, rollers, etc.
– Flush out debris, rebar fragments, etc. with increased water supply.
– Ensure barrel is aligned and centred on drill spindle.
Overheating commonly occurs when drilling harder materials and to insufficient water reaching the drilling area.
– Enhance water flow both through the core and around the sides of the drill, directing it toward the drilling area for improved cooling and lubrication.
Core bit segments can fall off due to various reasons. These include an incorrect bond, excessive bouncing, overheating, insecure anchoring, hitting loose rebar, or starting the drilling process at high speed. Identifying and addressing these issues is essential for maintaining safe and effective core drilling.
– Lower speed or use a core bit with a softer bond.
– Increase water supply.
– Hold the drill firmly or mount it on a stand.
– Flush out debris, rebar fragments, etc. with increased water supply.
– Tighten anchor or check vacuum pressure.
– Decrease RPM until rebar is cut and increase water flow.
– Start with a lower speed and gradually increase it.
– To remove a core bit segment from the material, wedge a chisel in the concrete. Tap gently to create space, and then pry out the segment using either air pressure, water lubricant, or a screwdriver before resuming the cutting process.
Uneven drill holes can occur when the material being drilled or the drill itself vibrates; this is evident when the core bit is vibrating and the material is in motion.
– Ensure the machine is mounted correctly onto the drill rig/stand and the core bit is tightly connected to the machine.
– Check the machine’s condition and replace worn parts if needed.
Could not find the support you need? Please contact our head office.
E: sales@syntecsolution.com
T: (866) 360-3607 or (760) 737-7407
F: (760) 737-6718
Our guide provides information that is for reference only. It is not a substitute for professional advice, and we cannot guarantee its accuracy. We recommend that users exercise discretion and seek guidance from qualified professionals. We are not liable for any loss or damage from using this guide. All descriptions, specifications, illustrations, drawings, data, dimensions and weights in this publication and all technical literature and websites containing information from Syntec Diamond Tools are approximations only. Syntec intends them to be a general description for information and identification purposes and does not create a sale by description. Syntec reserves the right at any time to:
a) Supply goods with such minor modifications from its drawings and specifications as it sees fit; and
b) Alter specifications shown in its literature to reflect changes made after the date of such publication.
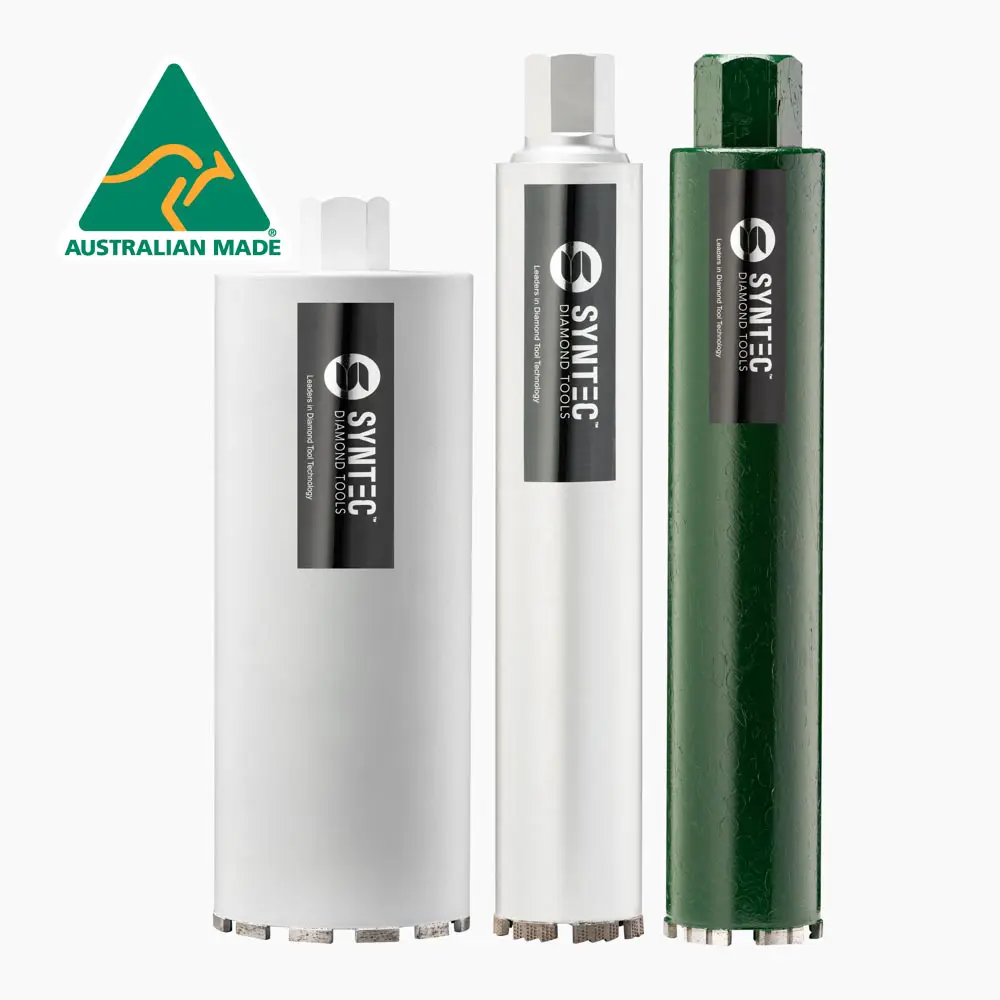
Request a Quote
Syntec Diamond Tools develop state of the art segments that cut faster and last longer than the competition. Construction professionals around the world trust Syntec Diamond Tools to provide them with the best coring solutions.